vacuum gas quenching furnace Horizontal with single chamber
What’s vacuum gas quenching
Vacuum gas quenching is the process of heating the workpiece under vacuum, and then cooling it quickly in the cooling gas with high pressure and high flow rate, so as to improve the surface hardness of the workpiece.
Compared with ordinary gas quenching, oil quenching and salt bath quenching, vacuum high-pressure gas quenching has obvious advantages: good surface quality, no oxidation and no carburization; Good quenching uniformity and small workpiece deformation; Good controllability of quenching strength and controllable cooling rate; High productivity, saving the cleaning work after quenching; No environmental pollution.
There are many materials suitable for vacuum high-pressure gas quenching, mainly including: high-speed steel (such as cutting tools, metal molds, dies, gauges, bearings for jet engines), tool steel (clock parts, fixtures, presses), die steel, bearing steel, etc.
Paijin Vacuum gas quenching furnace is a vacuum furnace consisted by furnace body,heating chamber,hot mixing fan,vacuum system,gas filling system,vacuum partial pressure system,electric control system,water cooling system, gas quenching system, pneumatic system,automatic furnace feeding trolley and power supply system.
Application
Paijin Vacuum gas quenching furnace is suitable for quenching treatment of materials such as die steel, high-speed steel, stainless steel, etc; solution treatment of materials such as stainless steel, titanium and titanium alloy; annealing treatment and tempering treatment of various magnetic materials; and can be used for vacuum brazing and vacuum sintering.
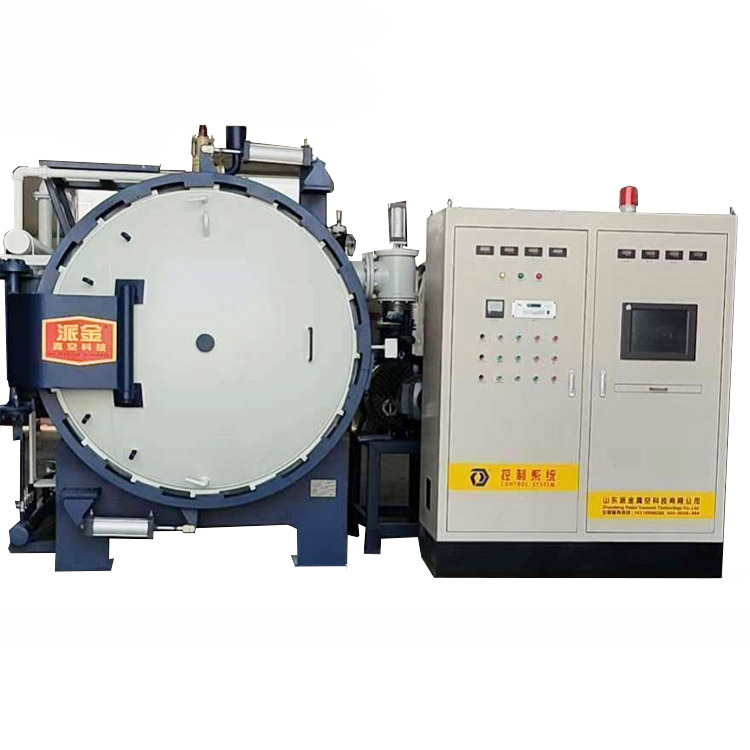
Characteristics
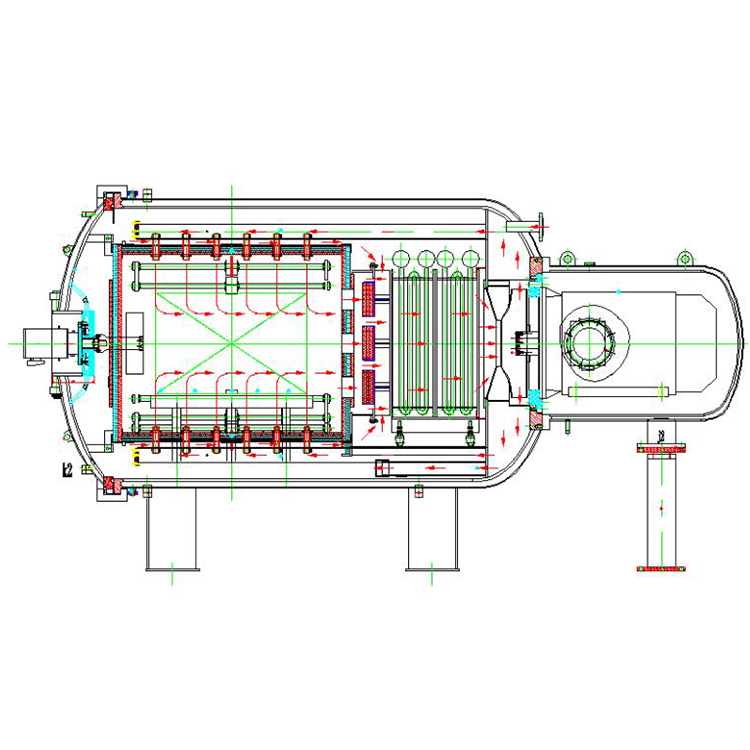
1. High cooling speed: by using high efficiency square heat exchanger, its cooling rate is increased by 80%.
2. Good cooling uniformity: Air nozzles are evenly and staggered set all around the heating chamber.
3.High Energy Saving: Its air nozzles will automatically close in heating process, makes its energy cost 40% less.
4. Better temperature uniformity: its heating elements are evenly set all around the heating chamber.
5. Suitable for various process environments: Its heating chamber’s insulation layer is made by composite hard insulating layer or metal insulating screen, suitable for various environments.
6. Smart and easy for process programming, stable and reliable mechanical action, automatically, semi-automatically or manually alarming and displaying the faults.
7. Frequency conversion control gas quenching fan, optional convection air heating, optional 9 points temperature survey, partial pressure quenching and isothermal quenching.
8. With whole AI control system and an extra manual operating system.
Standard model specification and parameters
Standard model specification and parameters | |||||
Model | PJ-Q557 | PJ-Q669 | PJ-Q7711 | PJ-Q8812 | PJ-Q9916 |
Effective Hot Zone LWH (mm) | 500*500 * 700 | 600*600 * 900 | 700*700 * 1100 | 800*800 * 1200 | 900*900 * 1600 |
Load Weight(kg) | 300 | 500 | 800 | 1200 | 2000 |
Maximum Temperature(℃) | 1350 | ||||
Temperature control accuracy(℃) | ±1 | ||||
Furnace temperature uniformity(℃) | ±5 | ||||
Maximum Vacuum Degree(Pa) | 4.0 * E -1 | ||||
Pressure raise rate (Pa/H) | ≤ 0.5 | ||||
Gas quenching pressure (Bar) | 10 | ||||
Furnace structure | Horizontal, single chamber | ||||
Furnace door opening method | Hinge type | ||||
Heating elements | Graphit heating elements | ||||
Heating chamber | Composition structure of Graphit hard felt and soft felt | ||||
Gas quenching flow type | Vertical alternating flow | ||||
PLC & Electric elements | Siemens | ||||
Temperature controller | EUROTHERM | ||||
Vacuum pump | Mechanical pump and roots pump |
Customized optional ranges |
|||||
Maximum temperature |
600-2800 ℃ |
||||
Maximum temperature degree |
6.7 * E -3 Pa |
||||
Gas quenching pressure |
6-20 Bar |
||||
Furnace structure |
Horizontal,Vertical, single chamber or multi chambers |
||||
Door opening method |
Hinge type, Lifting type,Flat type |
||||
Heating elements |
Graphit heating elements, Mo heating elements |
||||
Heating chamber |
Composed Graphite felt, All metal reflecting screen |
||||
Gas quenching flow type |
Honrizontal alternating gas flow;Vertical alternating gas flow |
||||
Vacuum pumps |
Mechanical pump and roots pump; Mechanical, roots and diffusion pumps |
||||
PLC & Electric elements |
Siemens;Omron;Mitsubishi;Siemens |
||||
Temperature controller |
EUROTHERM;SHIMADEN |
Quality control
Quality is the spirit of the products, is the key point decide a factory’s future.Paijin take quality as the most priority issues in our daily work.To ensure the good quality of our products, we paid much attention on 3 aspects.
1.Most important: Human. Human is the most important point in every work. We have complete training courses for every new worker, and we have rating system to rate every worker to a level (junior, middle, high), different level workers are apponted to different jobs with different salary. In this rating system, it’s not only the skills, but also rate in responsibility and error rate, executive power etc. By this way, workers in our factory are willing to do the best in his work.And strictly follows the quality management rules.
2. Best materials and components: We only purchase the best materials on market, we know that saves 1 dollar in material would cost 1000 dollars in final. The key parts like electric components and pumps are all brand products like Siemens, Omron,Eurotherm, Schneider etc. For the other parts made in China, we choose the best factory in industry and signed product quality guranntee contract with them,to ensure every component every parts we use in the furnace is the best quality products.
3. Strict Quality management: We have 8 quality check points in the processes of furnace producing, Examination in each check point is carried by 2 workers and 1 factory manager is responsible for it. In these check points, materials and components, and every aspects of the furnace are double checked to ensure its quality. At last, before the furnace leaves factory, it should be final checked with heat treatment experiments.
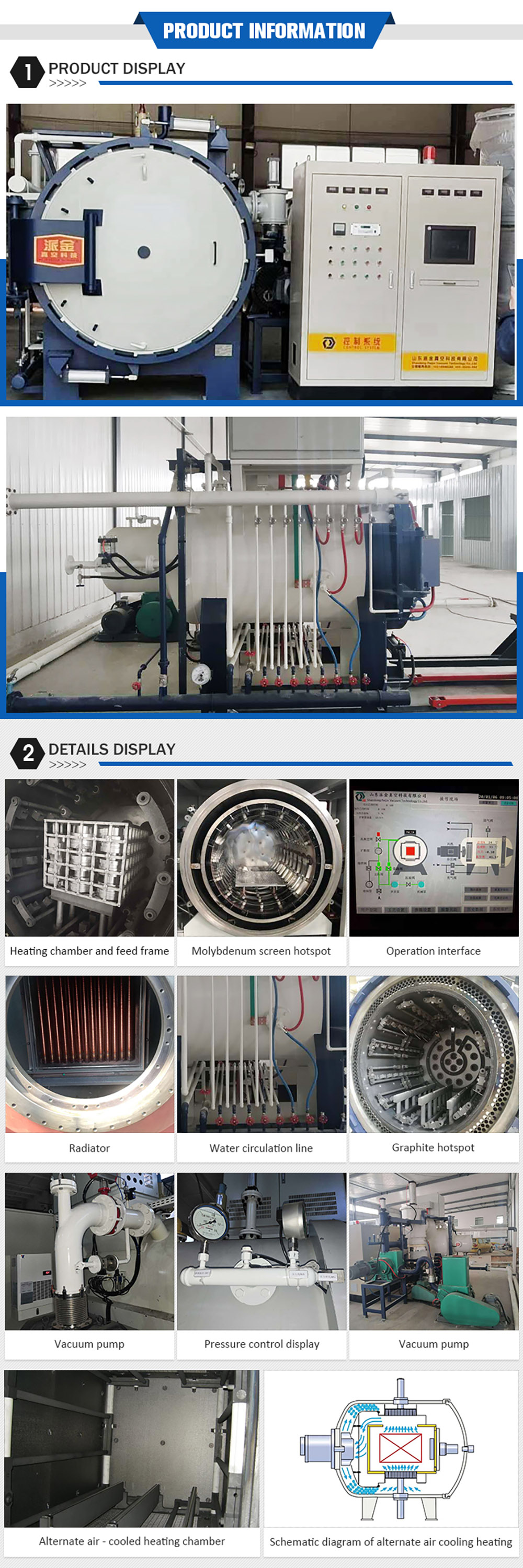
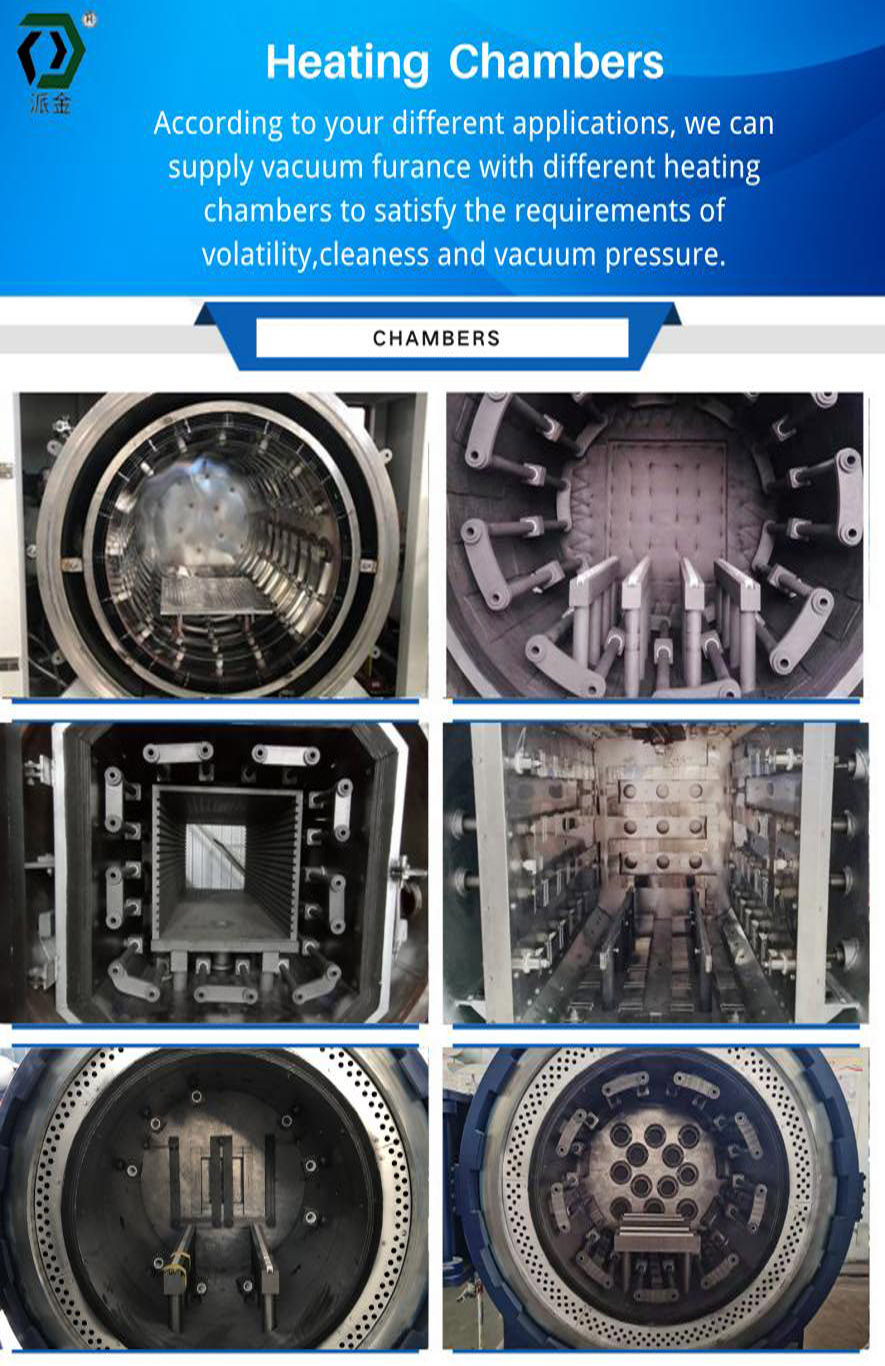
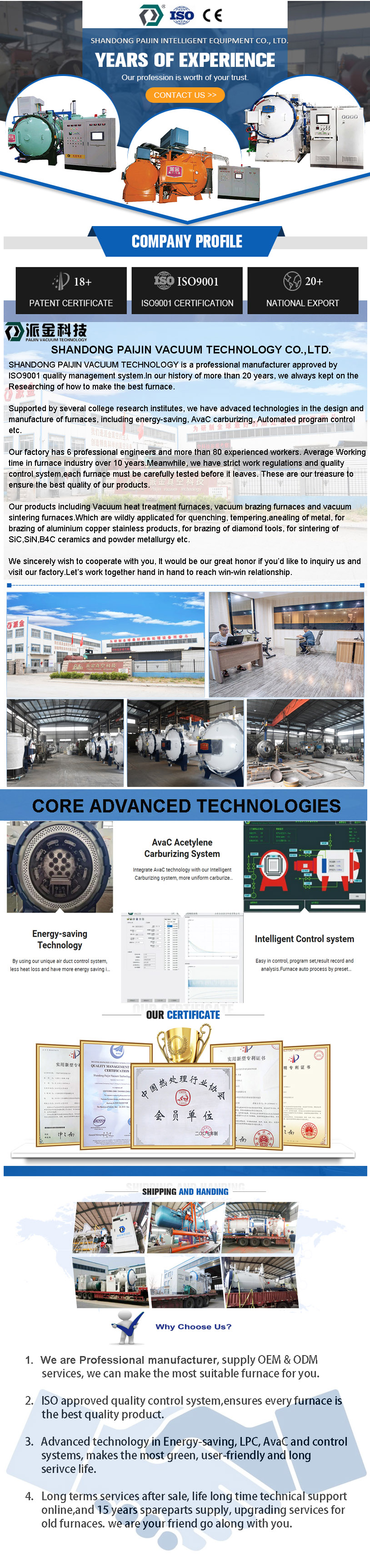